Pottery - introduction
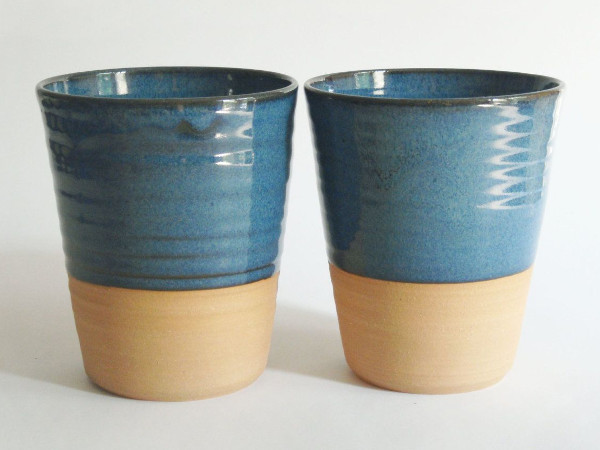
“I thought clay must feel happy in the good potter’s hand.” – Janet Fitch, White Oleander
Contents
What is pottery?
It’s using clay to make pots and other items – food and drink containers, flower pots, tiles, ornaments etc. There are various methods of making pots, after which they have to be dried and then fired (heated to a high temperature) in a kiln. After firing, the clay becomes ceramic, which is hard, and doesn’t break down in contact with water, as unfired clay would. Patterns and colours can be introduced onto the pot by scratching, painting, printing or via transfers. Pottery for use with food and drink has to be glazed, otherwise it will be porous and unhygienic.
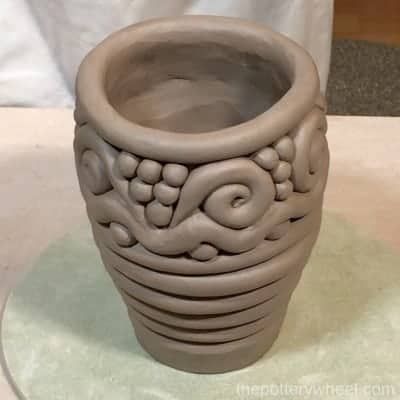
Clays
Clays are extremely fine-grained soils formed by the chemical weathering of rocks. Primary clays, or kaolins, are found at the site of their formation. Secondary clays have been moved by wind, water or ice. The movement reduces particle sizes and makes the clay smoother, and it picks up impurities that change its colour and lower its firing temperature. Ceramics, such as earthenware, stoneware and porcelain are classified according to the type of clays used and firing temperatures.
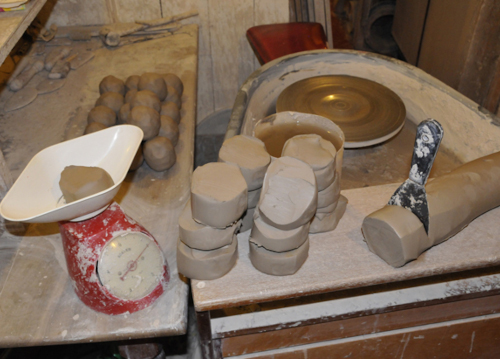
History
Pottery is one of the oldest human technologies. Ceramic figures have been found that are almost 30,000 years old, and fragments of pots have been found in Japan, in deposits dated around 14,000BCE. The potter’s wheel is also an ancient invention – around 3-3500BCE in the Indus Valley, China, Egypt and Mesopotamia. No-one’s sure who was first; but the potter’s wheel wasn’t invented in the Americas at all.
Techniques
Hand-building – easier than using a wheel. The main methods are coiling, pinch pots, slab pots, rolling and wrapping or press-moulding (see below). Then there is ‘throwing’ – i.e. making a pot on a potter’s wheel. This method needs a lot of practice.
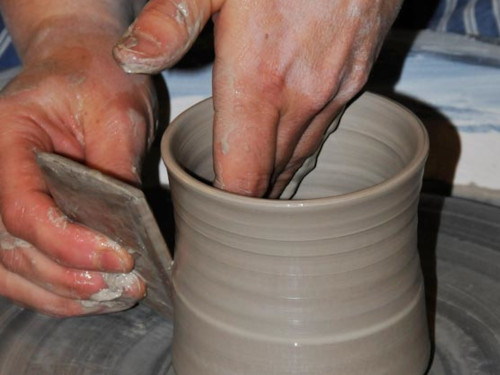
Firing and glazing
Kilns can be electric, gas, coal- or wood-fired. There are two types of firing: bisque firing turns your clay pot into a hard, ceramic pot, after which you glaze it and back it goes into the kiln for the glaze firing. Glaze is a silicon-based material in liquid or powder form that is applied to pottery to make it non-porous, but also for decoration. Glaze contains silica (the glass), alumina (clay to make it stick to the side of the pot) and flux to lower the melting temperature of the silica (from 1700°C, which is too high). Firing makes it set hard as a protective layer.
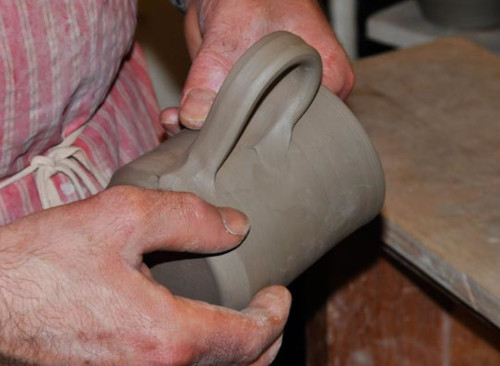
What are the benefits of making pottery?
- You can learn to make your own useful and beautiful items, which can be therapeutic, and you can gain the skills to start your own small business. If you don’t want to make your own, you can buy your ceramic items from a local potter, if you have one. They’ll be more expensive, but barring accidents, they will last a lifetime. You’re also supporting your local economy, rather than multinationals importing cheap, sweat-shop mugs and plates from the other side of the world, with all the pollution and carbon emissions that that entails.
- The most environmentally-friendly way of making your own pottery is by using locally-dug clay, handbuilding or using a kickwheel and a wood-fired kiln – or you can go a step further and hand-build ‘wild pottery‘ from hand-dug clay, fired on an open fire, and glazed with milk.
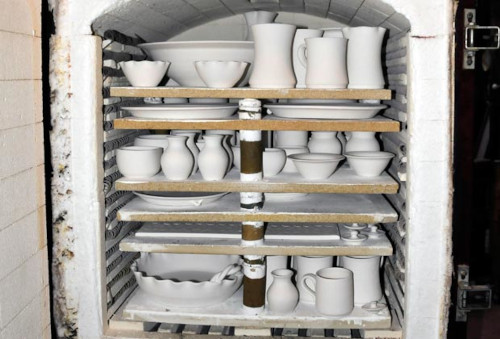
However
- Ideally, pottery kilns are not something for the household scale. Several houses in a community having a pottery kiln makes no sense, environmentally. A kiln is something that lends itself to the community scale – i.e. one kiln in a community serving several potters, who can fire their work at the same time. Lots of other low-impact topics are best suited to the community scale too.
- The price of local craft goods will be problematic for working people, but a) if the worst happens, and long supply chains break, we’ll need local people with the skills to make pottery or, well, we won’t have pottery; b) local people can be producers as well as consumers, and so can receive good prices for their products and services, in which case they can support other local producers; and c) as we grow the commons economy, it will reduce the cost of housing, utilities etc, so that people have more to spend on good-quality local produce, and it will take customers, money and power away from the exploitative corporate sector, and their ability to undercut local producers / growers etc. with shoddy goods and low-nutrition food will be reduced.
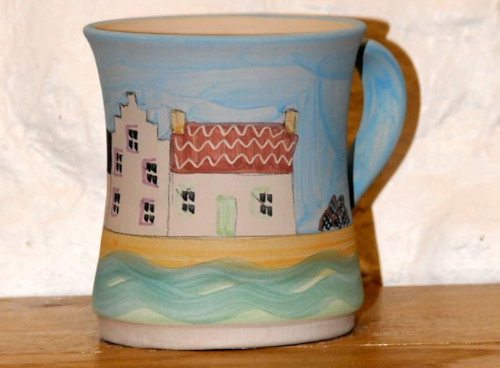
What can I do?
Pottery isn’t something you can learn only from books. You have to have a go – see the Craft Potters Association for pottery courses near you. There are also lots of free how-to guides here, and free online classes and videos here.
You could also just try and dig up some clay, and experiment – see if you can make pots with it, and see if it fires at an appropriate temperature. If you can’t find local clay, you can buy everything you need from potters’ suppliers. First prepare your clay, by wedging and kneading to get rid of air bubbles. Then have a go at the different techniques.
Hand building
- Coiling – you can make different shapes using long, rolled pieces of clay and building up from the bottom. Coiled pots are done in stages – do the bottom part on day one, build it a little higher on day two, and finish it on day three, unless it’s a large pot, and you can continue for a few more days.
- Pinch pots – made from a single ball of clay, by pinching the sides up.
- Slab pots – with square/rectangular base and sides.
- Press-moulding – the clay is rolled out flat and pressed into (or around) a mould to make shallow dishes.
- Just rolling out the clay and wrapping it around ready-made shapes or tubes to form vases, for example; you can make square shapes as well.
These techniques can be combined on single items. You can press designs into the clay when it’s wet, and scratch patterns when it’s ‘leather hard’ – the tidying-up stage. Then leave to dry before firing.
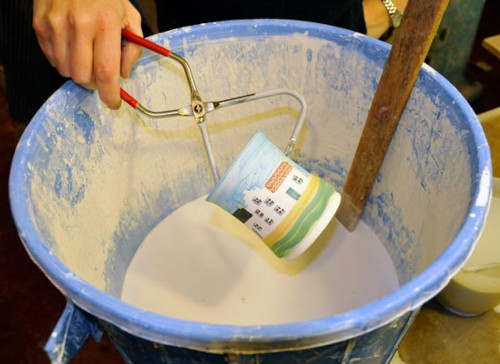
Throwing
First you need a potter’s wheel, from a potters’ suppliers, or second-hand. If you’re sure you’re going to continue pottery, make sure you choose a good-quality wheel though, because if you do, it will last a lifetime. Well actually, a kickwheel will last a lifetime, and is more environmentally-friendly than an electric wheel, as it’s spun by leg-power rather than electricity. You can also build your own wheel. You can adapt almost anything that spins – like a bicycle wheel. You’ll find lots of ideas on how to do it on YouTube.
1lb (0.5kg) of clay will give you a mug or a small bowl, but you’ll know how much clay to use with practice. Form the clay into a ball, put it onto the wheel and do a bit of ‘coning and balling’ – squeezing up and pushing down to prepare the clay for throwing. Make sure the clay is centred by turning it a few times, then stick your thumb in the top to open up a hole, before turning the wheel and bringing up the clay at the sides with your hands (this is the most difficult part for beginners). Master small pieces first before moving on to bigger items.
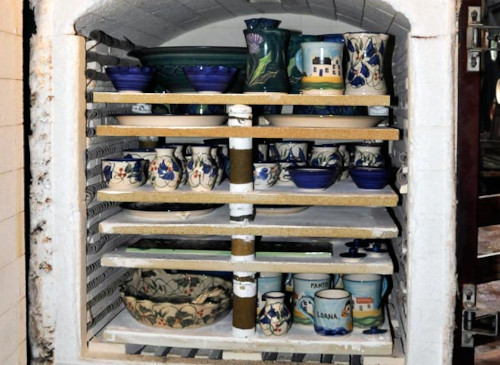
Put your pot aside, and when it’s ‘leather hard’, put it back on the wheel to trim off excess clay from the bottom and to tidy up the outside. Then make your handle if necessary – score it where it joins the pot/mug and fix using slip (watered-down clay).
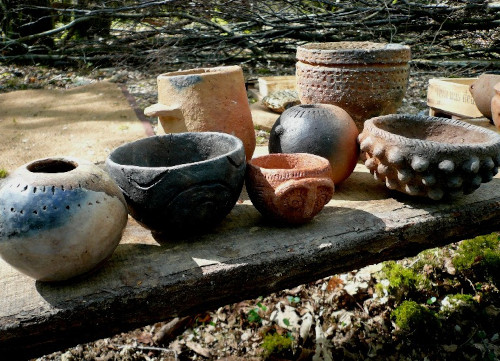
Drying, firing and glazing
Your pot can crack if it dries unevenly, which may happen if it’s not the same thickness throughout. Items have to be bone-dry before firing, which usually means leaving them on a shelf for a week. Kilns are expensive, but there are lots of places you can hire kiln time to fire your pieces – do an online search for your town or search your local classifieds. Earthenware is usually fired in the temperature range 1000-1200°C, stoneware 1100-1300°C and porcelain 1200-1400°C.
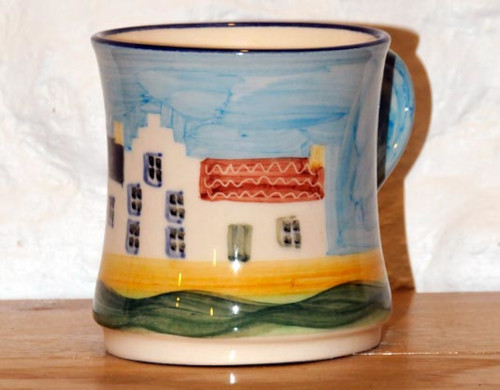
You don’t know what you’re going to find when you open the kiln. Hopefully everything will have gone well, but your pot may have cracked, or even blown up if there was air in the clay. You can also fire ‘wild pottery’ on an open fire or in a pit (see ‘benefits’, above).
There’s an enormous amount of information that’s beyond the scope of this introduction – such as:
- various types of glazes, including shiny, matt, dry and raku.
- salt or sugar firing – thrown into the kiln at peak temperature to give an ‘orange peel’ effect.
- oxidation (allowing air in) and reduction (keeping air out) glaze firing, to produce different colours and effects.
- raku firing, at lower temperatures for a lustred appearance.
But these and more can all be learnt after you’ve mastered the basics.
Specialist(s)
Thanks to Shirley Stewart for information and Crail Pottery for photos.
The specialist(s) below will respond to queries on this topic. Please comment in the box at the bottom of the page.
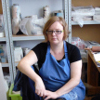
Fiona Thompson is a ceramic artist based in Edinburgh. She has been making and exhibiting ceramics since studying in the mid 1990s, as well as teaching and numerous other projects. She set up Cyan Clayworks in 2012, a social enterprise and working studio which provides workspace, courses, tuition and studio hire for adults.
4 Comments
How pollution can be stopped while making pots in the furnaces?
Hi Aman. Either we fire pottery, or we don’t have pottery I guess. Don’t know what we’d do then. There’s a lot we can do – i.e. find more sustainable ways to fuel kilns – there’s a link to ‘wild pottery’ techniques in the article; or wood-fired kilns; plus just use less pottery. Most houses have way more cups, mugs, plates, bowls etc. than they ever use, I find. But I guess that’s a systemic problem – humans use too much of everything, and tend to aspire to more each year, as that’s what they’re persuaded to do by the advertising industry. I guess using computers / the internet is as ecologically-damaging as firing pottery – more so because of the scale involved, presumably.
Hi Aman, its a complex area…Dave has covered it pretty well in his comment. Those of us that make ceramics or pottery in a studio setting do as much as we can to make sure the kiln is as full as possible before firing, and newer electric kilns are very efficient. Hand made pots, whether functional or decorative/sculptural, are however a much more sustainable purchase than most disposable design…buy a good quality handmade mug for example, and it could outlast its owner. Some individual potters and artists are working on making their studio practice as environmentally friendly as possible- digging and processing their own clay and even glaze materials.
Hi Shirley, enjoyed your presentation on this page on what sort of products you help beginners to produce. I am interested in amphora water containers and therefore i am interested in your comments if any on this please ?
yours sincerely Paul Bennett