“Your DIY jewellery making skills will come in handy when you want to gift a friend something handmade or even when you want to unwind and indulge in a little creative time.” – Sameer Mehta
Contents
What is jewellery making?
Jewellery making is the art of making decorative items such as necklaces, bracelets, brooches, ear, nose, finger and toe rings, etc. to wear on the body or on clothing. The practice of body adornment may be almost as old as humans. There’s evidence that, long before the discovery of precious metal deposits and the development of metalworking skills, prehistoric peoples made jewellery from shells, stones and bones.
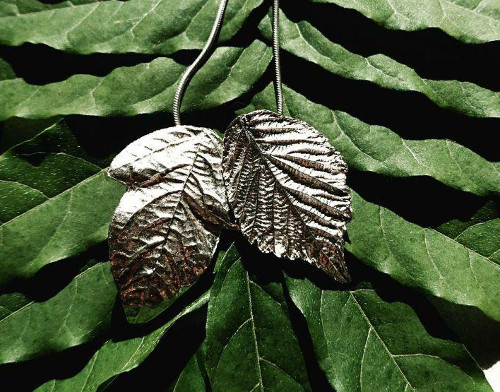
Beyond its intrinsic aesthetic or economic value, jewellery has traditionally been used by different cultures down the ages as a mark of rank, status, power and wealth, as well for its talismanic and symbolic properties. Great civilizations like the ancient Egyptians and Romans buried splendid, elaborate pieces with the dead, and the wearing of amulets or certain stones in many cultures was (and still is to an extent) to bring luck, ward off evil or protect against ailments. While jewellery today can be made out of almost anything, precious metals like gold, silver and platinum, often combined with gemstones, dominated jewellery making for many centuries. Expanding global trade (and a lot of theft from colonies) in the 17th and 18th centuries fuelled the European appetite for pearls and gems and saw brilliant cut diamonds eclipse other stones in popularity.
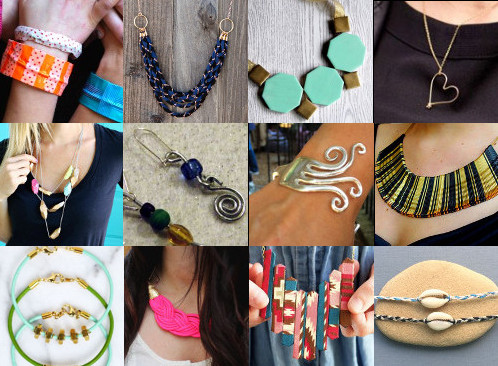
The use of jewellery as a status symbol began to decline somewhat during the Industrial Revolution when the invention of gold plating and imitation stones made it more affordable and readily available to all. The Arts and Crafts movement, with its naturally-inspired shapes and designs, promoted a revival of hand crafting techniques, while the ‘machine age’ of the 20th century ushered in the use of modern new materials such as Bakelite and plastics.
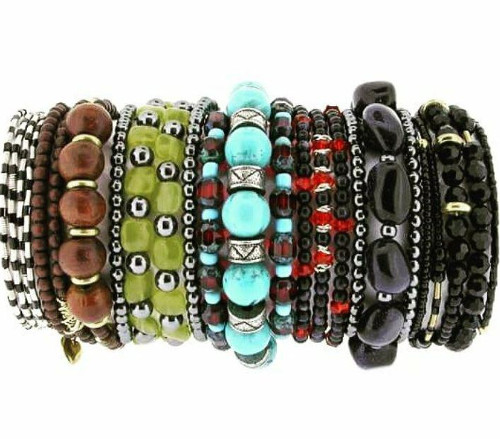
What are the benefits of jewellery making?
For such pretty adornment, the jewellery industry can be very ugly. Most of it is sold at hugely inflated prices, little of which makes its way back to the country of origin. It also comes with a hefty price tag in the form of human and labour rights abuses and environmental damage. Precious metals and gemstones are often sourced from developing countries, with substandard working conditions, low wages and unenforceable health & safety regulations, and the involvement of underage workers in sweatshop conditions is not uncommon. Mining for precious metals like gold, silver and platinum is one of the most environmentally-damaging industries in the world, responsible for displacing indigenous communities, destroying pristine environments, polluting land and water with substances like mercury or cyanide, damaging human health, devastating wildlife, leaving open scars on the land and generating huge amounts of waste. An oft-quoted figure by campaigners against ‘dirty gold’ is the 20 tonnes of waste it takes to produce one standard gold wedding ring. And all of that is before you even factor in the highly-polluting, energy-hungry smelting and refining processes.
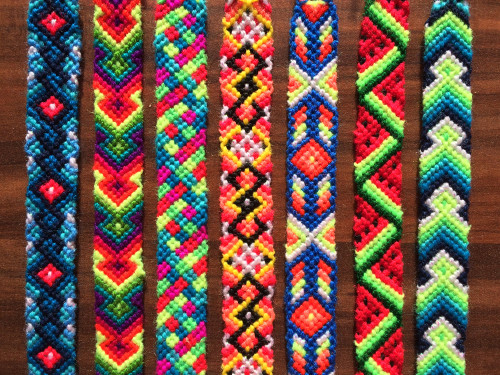
Glittering gems also hide a dark side: ‘conflict’ or ‘blood’ diamonds and other stones, often sourced by forced labour and in terrible conditions, have been used to fund crippling wars and insurgencies in countries like Sierra Leone and Angola in recent years.
Things are slowly improving though: consumers are becoming more aware and organisations like Ethical Metalsmiths, the Kimberley Process and the Responsible Jewellery Council are working towards improving pay and conditions for workers in source countries and avoiding the use of conflict stones. It’s now possible to source precious metals from the world’s few Fair Trade mines. However, the metals supply chain can be convoluted, particularly if items are sent for re-smelting or bought from a casting house. Even with the best intentions it can be hard for a retailer to ensure that a piece of jewellery is 100% ethical. By contrast, gemstones are a bit more straightforward as they don’t tend to be re-cut when reused and thanks to the Kimberly Process it’s now possible to find trusted suppliers who offer written conflict-free guarantees.
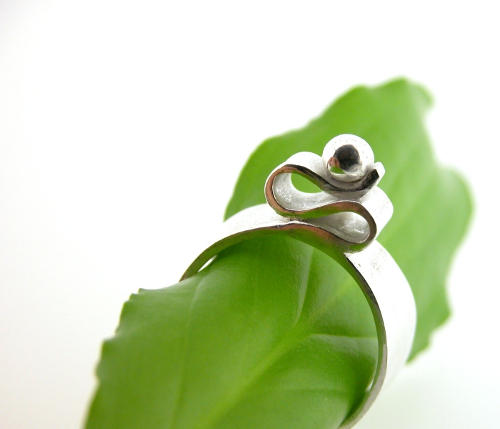
You can reduce the impact of your jewellery by buying either original or ‘upcycled’ items from an ethical local designer; or you can learn to make your own. These options have a number of advantages:
- You can get an original, unique item made just for you. Or you can give pre-loved or broken jewellery a new lease of life. For example, an old, broken necklace could be made into a bracelet and a pair of earrings. Many people scrap old jewellery, which is a shame and entirely unnecessary as much of it can be repaired or reworked. Stones in particular are endlessly recyclable and, with some limitations, precious metals can continually be melted down and recast. Upcycled jewellery (nb: upcycling is using old objects again; recycling is crushing / melting / destroying old things to make new things) also has the potential to incorporate a huge range of materials and styles and be highly eclectic and individual.
- Spending money locally means that it stays in your community, rather than being taken out by corporate jewellers to pay shareholders.
- Fully localised production also ensures that no manufacturing stages are outsourced overseas to maximise profit at the expense of workers’ pay and conditions.
- The carbon footprint of your jewellery is greatly reduced as there’s no overseas shipping.
- Energy use when working with recycled materials is pretty much the same as with raw, but you avoid (or at least spread) the impact of the mining and refining processes.
What can I do?
You can support ethical and/or local suppliers and makers. Look for jewellery makers who offer repair or upcycling services where you can take your old, odd or broken items in to be repaired or melted down or otherwise reworked. Things like ear wires, piercings or any pieces of jewellery which have been inserted into the skin are usually off limits for hygiene reasons (unless melted down) but other than that the only limits are your budget and your imagination. Whether you’re buying an original or a recycled piece, don’t be afraid to ask your maker about their source materials and production methods. A good designer will happily talk to you and may even allow you watch certain stages of the production process.
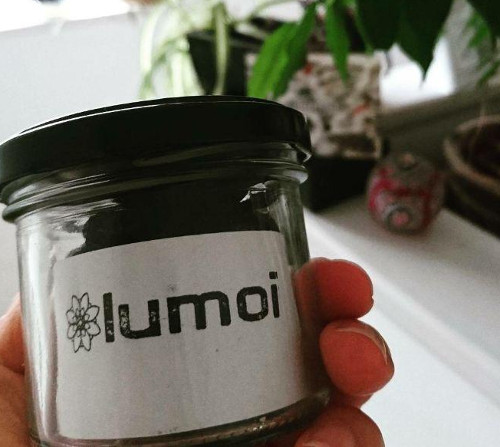
You can also learn to make your own jewellery from re-melted and recycled metals, precious and non-precious stones, old cutlery, crockery, textiles, wood and driftwood, beads, plastics, even car tyres. Precious metal clay (PMC) is a popular low-impact material made from finely ground pure silver particles reclaimed from scraps, x-ray and film plates which can be shaped and moulded by hand or with tools.
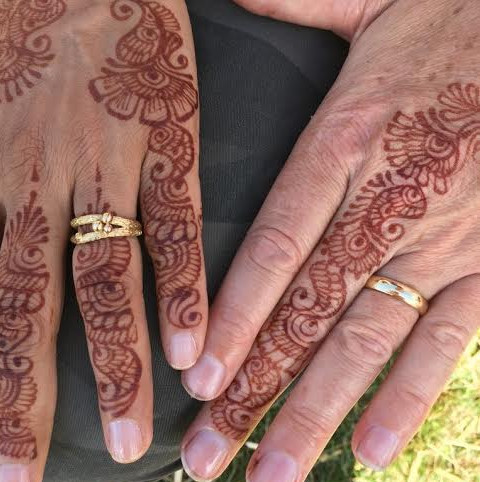
If you want to learn to make your own jewellery you can take an introductory course with a local jewellery school or art college to get a feel for it, and it’s also perfectly possible teach yourself using books and the Internet. A search for ‘jewellery making projects’ will return thousands of free online tutorials or beginner’s projects. You can pick up a basic jewellery-making kit for just a few pounds online with all the wire, strings and fittings you need to get started.
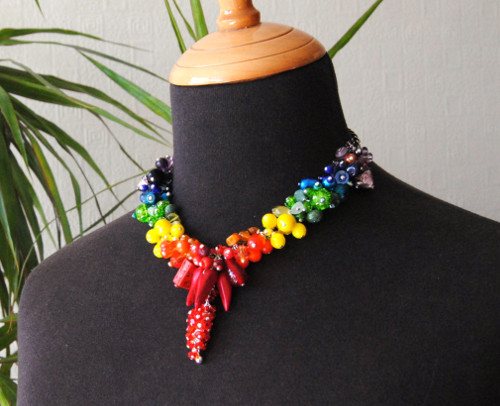
If you’re interested in pursuing a career at the high end of jewellery making, the usual route is to study at art college or similar and go on to an apprenticeship lasting several years. Apprentices aren’t well paid, so budding jewellery makers tend to start young. However, the Goldsmiths’ Company funds training and helps put employers and apprentices together, so at least you’re not saddled with student debt. Post-apprenticeship, you may decide to stay on with the company or to rent a bench in a shared workshop, giving you access to the necessary machinery without the high costs of setting up your own workshop: around £80,000-£100,000 for initial tools and stock, plus rent and insurance (at this end of the market, jewellery is a high-value / high-risk business so premiums are high).
Specialist(s)
Thanks to Louise Kane of Readorn and Richard Talman of RTFJ for information.
The specialist(s) below will respond to queries on this topic. Please comment in the box at the bottom of the page.
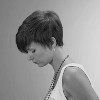
Louise Kane has worked in the jewellery industry since 2004, and in 2008 she formed Readorn, providing an eclectic mix of handmade jewellery from recycled silver and reused/upcycled materials. She believes that all materials hold value; nothing should go to waste; beautiful things don’t need to cost the earth; sustainability isn’t just another trend; and being resourceful is vital for our future.
2 Comments
This is really good to know – I’m thinking of making gemstone/crystal jewellery (very simple stuff; pendants mostly) and selling it to supplement my income…a good reminder about ethical traceability.
I really like this DIY necklace jewellery. I think, I really enjoy making this. Thanks for sharing cool DIY.