“Felt is an ancient craft, dating back to the Bronze Age. It is the oldest textile fabric and was made before people learned to spin, weave or knit.” – Gillian Harris
Contents
What is felt making?
Felt making is making fabric by locking together fibres (generally wool) using friction and moisture. This is the traditional ‘wet’ felting technique, although now there’s also needle felting, which doesn’t require moisture or friction. Felt is probably the world’s oldest textile.
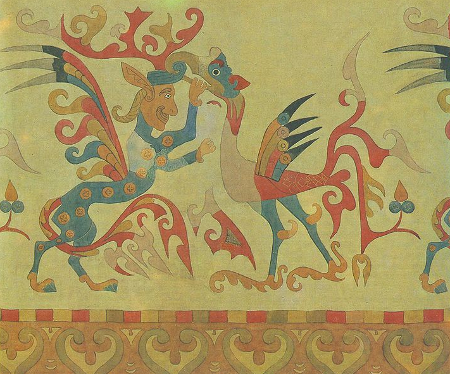
Wet felting
Hot, soapy water and friction are used to mat, compress and fuse wool or other animal fibres together to make felt.
Nuno felting is a type of wet felting, where wool is felted onto a woven fabric. The wool fibres are worked through the weave, which gives the felt the stability of the woven fabric. This technique is great for upcycling old clothes.
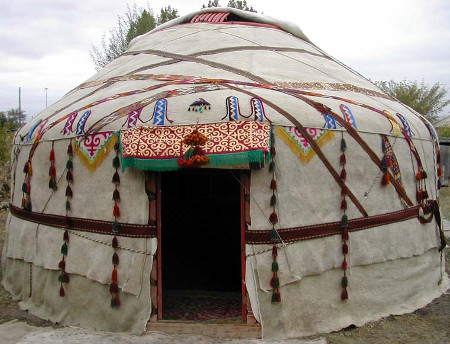
Needle felting
Interestingly, needle felting as a craft developed from an industrial process, rather than the other way around. The technique developed within the last 100 years, with triangular-shaped needles with notches that push and intermingle the wool fibres to create felt – no water or friction is required. Non-woven fabrics from piano felt to tennis balls are made this way.
History
Legend has it that felting was discovered when travellers put wool in their sandals to prevent blisters, and the combination of sweat and the friction of walking created basic felt socks!
It’s notoriously difficult to track the history of textiles, as they’re biodegradable. Something has to happen to preserve them. That’s exactly what happened to the felt found in the Pazyryk tombs, discovered in the permafrost of the Altai mountains in Siberia, near the Mongolian border. Water seeped in and cased everything in ice, so we can see what felt looked like around 2400 years ago. There are clothes, ornaments and rugs, and the workmanship is superb, suggesting that felt making began there a lot earlier than that.
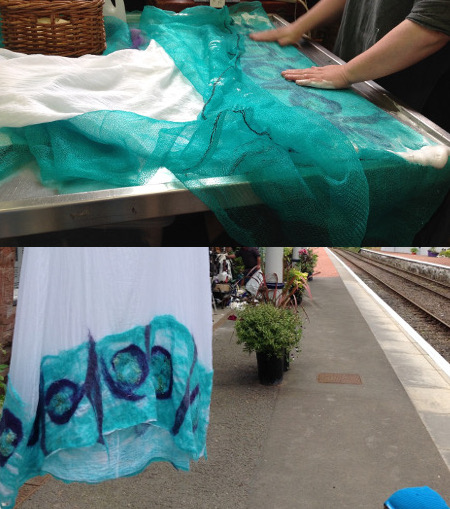
Mongolia is considered the home of felt making, although other central Asian countries like Kazakhstan or Kyrgyzstan have their own ancient traditions and techniques. Felted wool is traditionally used for yurt covers and insulation – unwashed, it’s dense enough and contains enough natural oils to be virtually waterproof in Mongolia’s relatively dry climate.
Felt making appears all over the world – anywhere there are sheep – but wet felting arrived relatively late in the UK. Mary Burkett, founder of the International Feltmakers Association, discovered felting in Persia and introduced it into the UK in the 20th century. Most sheep in the UK were traditionally owned by wealthy landowners who paid locals to spin and weave it – but not to wet felt it, as the skill was not known in the UK.

However, a technique that was known was ‘waulking’ – used to soften and shrink to make a denser, more waterproof fabric, like tweed. Putting a woolly jumper into a hot wash does a similar thing. Stale urine was used – the ammonia changed the pH of the wool, which opens up the scales of the fibres, then agitation makes the scales attach to each other.
Another industrial felting technique that developed before needle felting was sometimes called ‘carroting’ and was used to make hats. Rabbit fur was blown onto a mould and treated with a mercury compound that often caused mercury poisoning in milliners. Mercury poisoning can often cause brain damage – hence ‘mad as a hatter’. Don’t try this one at home.
What are the benefits of felt making?
Self-provisioning / personal
Gaining any craft skills can help meet your and your family’s needs, save you money and bring a lot of satisfaction and pleasure. Felting (and especially needle felting) can be very therapeutic, and the rubbing involved in wet felting can keep you fit.
Wool (and therefore felt) has two extremely important qualities – it has very low flammability and provides excellent insulation against both heat and cold (felt liners in boots and wellies will keep your feet warm in winter) – and against sound too.
If you enjoy it and are good at it, you could potentially gain an income or a job, by providing things for your community.
Decentralising power away from corporations
Providing things for ourselves in communities helps prevent extraction, decentralises power away from corporations (which makes it more difficult for them to corrupt democracy) and democratises work.
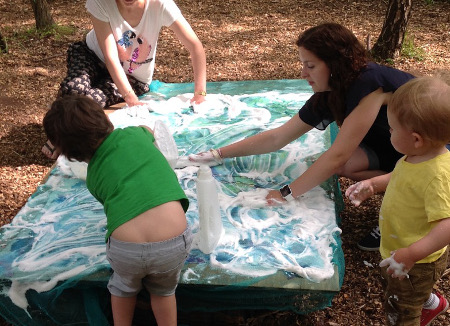
Building community and preparing for any potential collapse scenarios
In case of any kind of collapse scenario (broken supply chains, environmental destruction, financial crash, war, civil unrest etc.), we’re going to have to look after ourselves in our communities, and so the more people with useful skills the better.
The UK has over 60 registered sheep breeds. Many smallholders use sheep for conservation grazing as well as for meat and wool. Sheep are integral to lots of smallholdings and mixed farms, which are vital for resilient communities. However, wool has fallen in value so much that it is often considered a waste product these days. Anything that can add value to local British wool has to be a good thing.
Environmental
Felting can make use of a local resource, with short supply chains, where you can see the way it’s produced. It’s also renewable, biodegradable, repairable and recyclable if it all goes pear-shaped (a failed hat can become a tea cosy).
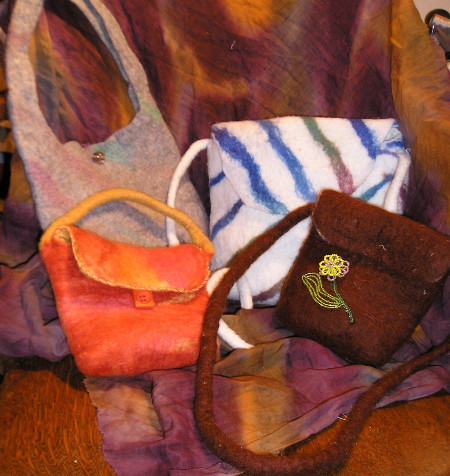
What can I do?
Felting can be used to make clothes, bags, hats, pictures, jewellery and 3-dimensional or stuffed objects like toys or waste baskets. You can also make felt rugs – the equivalent of sheepskin rugs, but without having to kill the sheep to get it. Wet felting is very easy, doesn’t need specialist kit and can be done with kids. Needle felting, on the other hand, involves sharp things and so may not be so good to do with kids. There are no right and wrong methods – however, there’s good and bad felting in terms of whether it’s useful for the purpose for which it was intended. For example, if you’re making a picture, it’s fine if it’s loosely felted, but if you’re going to use the same piece for a handbag, it will probably fall apart if it’s not tight felted or fulled (a cleansing and thickening process) enough. You can attend courses to learn general felting techniques or how to make specific items. You can find courses via the International Feltmakers Association. They run regional workshops and you can find out what’s happening in your area.

You can do wet felting on your kitchen table. Coarse wool takes longer to felt, so it’s probably best to start using finer wool. Use a net (debris netting from building sites works) / old vegetable sack / net curtain / bamboo mat placed on a towel. The washed, carded wool to be felted is placed on top of the net material. Small amounts are overlaid like roof tiles. Do it in a couple of layers – the second layer overlaid in the opposite direction to the first. Then either another piece of net (etc.) is placed on top, or it’s all folded over so that the wool is between two pieces of netting. Warm soapy water is rubbed in a circular motion. The rubbing creates friction and the water provides moisture to cause the wool to shrink and mat to create felt. See here and the first video above for more on the techniques of wet felting.
Needle felting allows you to use coarser wools that might not wet felt so easily. You can buy felting needles online – Wingham Wool Work and World of Wool (both in Yorkshire) are good sources, and there’s a lot of good information on those sites too. Needles are pushed backwards and forwards through the wool and into some sort of pad, so that you don’t stab yourself. You can learn needle felting on courses, or you can find instructional videos like the one above.
You can use a combination of wet felting and needle felting to mend clothes. For example, if you have a hole in a jumper or a sock, put some foam underneath the hole and put wool on the inside and on the outside of the material. Use a felting needle to push through both layers of wool to mingle the fibres, and afterwards, wet felt it to solidify and condense the wool to finish the repair.
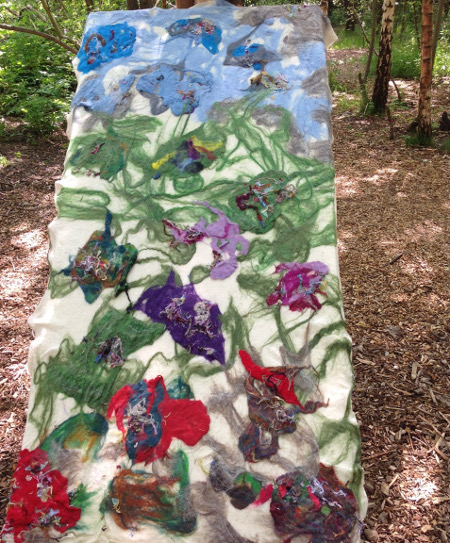
When you’re choosing fleeces to felt, remember that the wool from different breeds felts differently, and often, wool from the more rugged breeds (Scottish Blackface or Herdwick, for example) can be difficult to felt, or can produce coarse, heavy felt. Some breeds produce finer wool that’s easier to felt – like Bluefaced Leicester or Shetland. There are uses for the coarser wools though – Herdwick wool is often used in rope- or rug-making. But if you’re making something to be worn next to the skin, you’ll need the finer wools to make a soft felt. Merino wool is very good in this respect, but not much is produced in the UK. Most comes all the way from Australia – not a great idea, environmentally-speaking. Luckily, Bluefaced Leicester is very good too.
Further resources
- International Felt Makers Association – information, online courses, resources
- Complete guide to needle felting (25-page pdf)
- Niki Collier – free video tutorials
- Liz Gaffney – basic instructions for making a picture with wet felting
Specialist(s)
Thanks to Liz Gaffney of Heartfelt by Liz for information.
The specialist(s) below will respond to queries on this topic. Please comment in the box at the bottom of the page.
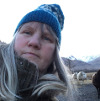
Liz Gaffney Whaite runs Heartfelt by Liz, and has been felting since 1996. She lives a simple life in Argyll in Scotland. Her studio is in a Victorian railway station where she and her husband keep sheep and work from fleece to finished garments. Liz dyes much of her wool from plants she grows herself. She offers felt making and botanical printing workshops throughout the year. They also have accommodation on the station platform.
2 Comments
I was researching glue as a possible sheep byproduct and read about the use of animal glue in sizing felt. What do you use to size your felt? Thank you for this wonderful article.
Hello Gail , thank you for your enquiry. . I use a water based millinery stiffener if I need to make my felt rigid and durable outdoors . It’s not a glue but a coating to the fibre . Lanolin would be the most likely byproduct to wool washing and it has all kind of uses , reproofing wool against moisture is a useful one ..The making of glue is a whole different process and one I don’t have much knowledge of.. I do believe that size from sheep skin is possible to process I hope that helps